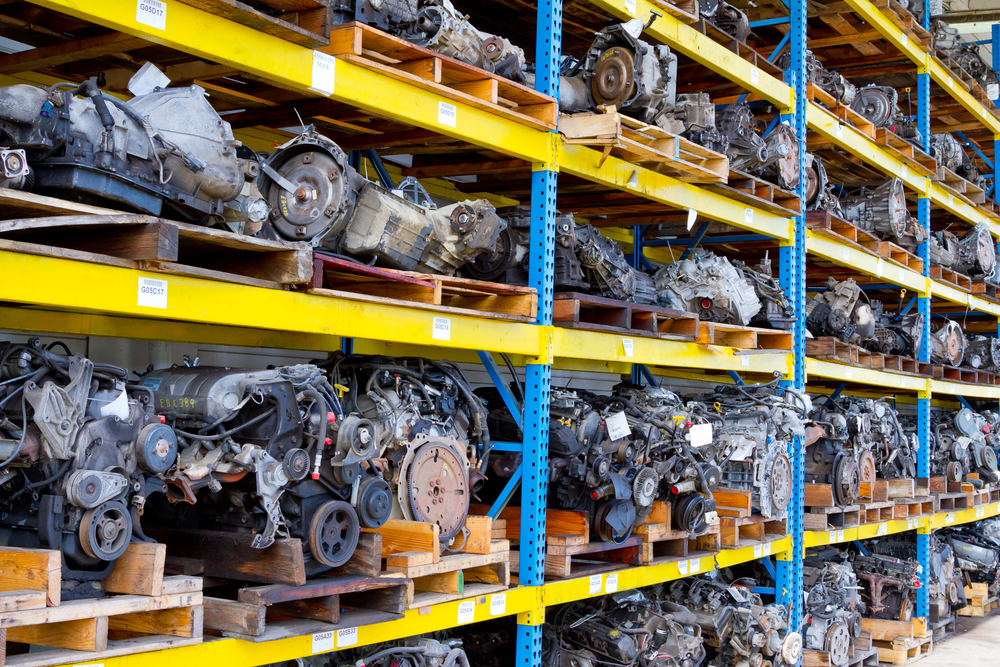
8 Ways To Better Manage Parts Inventory
The trucking industry is seeing a parts shortage. Although it started with the truck makers having trouble sourcing computer chips and other parts and components for their assembly lines, it is now rolling into the aftermarket, and fleets are experiencing wait times for replacement parts needed to complete maintenance service or repairs.
Having a truck waiting for parts is expensive. Each day of downtime costs a fleet $800 to $1,000, according to industry estimates.
It’s more important than ever for fleets to carefully manage their parts inventories. This helps ensure they have the right parts in stock when they need them. Good inventory management also means they won’t have unneeded parts in stock that will never be used.
Here are a few simple rules that will help fleets manage their inventories more effectively and even help them weather parts shortages.
Heavy Duty Trucking suggest the following solutions:
1. Use VMRS
To successfully manage a parts inventory, fleets need data. That’s where Vehicle Maintenance Reporting Standards come in.
“Managing inventory is easier if we can use VMRS coding of all types of information,” says Pete Russo, senior vice president of product strategy and innovation for Decisiv, a provider of asset service management. VMRS codes “normalize data,” he says.
The use of VMRS codes establishes standard part numbers regardless of the dealer or distributor the fleet uses to procure parts or the make and model of the vehicle.
2. Record all data
With VRMS codes as a base, all data related to maintenance and repair events needs to be gathered in one place so a fleet can see all the parts it has ever used.
“You need to know what you have, where it is at, what it cost, what you are using, and what you have on order,” Reynolds says.
In addition to capturing information on the parts used, also include information on the vehicle year, make, model, engine, and the number of miles or engine hours.
Also include the reason for the repair. Was it just a maintenance service, or was there a breakdown? Russo cautions, however, that including accident repairs may skew the data, as those are unplanned events.
3. Make records clean and accurate
Fleets should maintain clean and accurate computer inventory records.
“Part numbers need to be formatted consistently and match vendor’s part numbers,” Reynolds says. “VMRS numbers need to match VMRS standards. Quantity on hand and quantity on order need to match what is on the shelf plus open purchase orders. Part numbers need to have current bin locations. Costs need to be correct.”
Fleets also need to regularly perform a physical inventory count.
4. Set minimum stock levels
Each fleet should have a proactive plan to have critical parts on hand during good times and bad, according to Livingston.
“This minimal stock level will ensure against issues of the day, which will lead to more productivity and greater uptime for vehicles,” he says. “Work with your distribution partners to determine those critical parts needs and minimal level you should have. This inventory should be customized to your in-service vehicles.”
5. Forecast and make predictions
Two or three years ago, it was possible to look at the data captured from maintenance and repair events and spot breakdown trends. Today, thanks to artificial intelligence and machine learning, it is possible for fleets to look beyond trends to forecasting and predicting parts needs based on more variables.
“AI and machine learning allow fleets to take different variables into account and come up with better predictions about what parts they are going to need and when they are going to need them,” Decisiv’s Russo says.
6. Work with vendors
Parts vendors, whether dealers or distributors, can be a great asset in establishing ordering and delivery schedules.
“There is a general idea in the aftermarket channel that inventory may not be on the shelves at [local] brick and mortar locations,” says Daniel Griffin, senior director of aftermarket/digital solutions at Dana Aftermarket. However, the reality is — that at least in some instances — the part may exist in other locations. New technology allows suppliers such as Dana to give customers visibility into other places where a part may be.
7. Start small
It can seem daunting to undertake a technology project, but Decisiv’s Russo advises fleets not to bite off more than they can chew. “Start small and build confidence and expertise off of one project,” he says.
For example, a fleet might pick a certain application, region, or make of truck to gather and analyze data about a limited set of vehicles. Once the fleet gets initial results, Russo suggests relying on an industry expert to tell them if the results make sense and to validate their findings. Once results have been validated, the fleet can be assured it is collecting the proper data in the proper form and can be comfortable expanding the scope of the project.
8. Review periodically
Set-it-and-forget-it is not a good strategy when it comes to managing inventory. While it may initially be time-consuming to set up the database that allows the fleet to manage inventory, once it is in place, it becomes a simple matter of “reviewing it on a quarterly basis to look for exceptions and anomalies,” Russo says.
During a review, a fleet manager may notice that a certain type of breakdown is occurring more frequently, so stocking levels for parts associated with that repair may need to be changed. However, fleets should not have to make wholesale changes to what parts they keep in inventory and how many of each they have unless they make changes in their asset base.
Fleets also need to have some inventory controls in place to make sure “parts are not walking out the door,” Findlay says. “There are ways to minimize the 15% to 20% carrying costs through some common-sense fraud prevention controls.”
This article first appeared in the July 2021 print issue of Heavy Duty Trucking. Access the online article here.